Construction continues to change with new trends and techniques focusing on efficiency and accuracy. As urban projects increase in size, the need for quicker and dependable methods for concrete reinforcement is on the rise. The Rebar Threading Machine is one of the machines that assist in accomplishing this goal.
If you are a construction expert or new to the field, this guide on construction equipment will provide you everything on Rebar Threading Machines like their operations, merits, applications, maintenance, and how to select the finest model.
What is a Rebar Threading Machine?
A Rebar Threading Machine is a tool used in construction that performs the task of cutting threads on the ends of steel reinforcement bars. With these threads, mechanical couplers can hold two rebars together thus forming a joint. By doing this, it removes the bonding techniques known as lapping which is considered to be bulky along with unreliable.
Refurbishment of existing structures and erecting new ones often entails the use of threaded rebar connections which enables usage of skyscrapers, bridges, dams, and tunnels alongside other reinforced concrete structures. Furthermore, these connections allow for a higher tensile strength and allow loads to be transferred efficiently without breaking them.
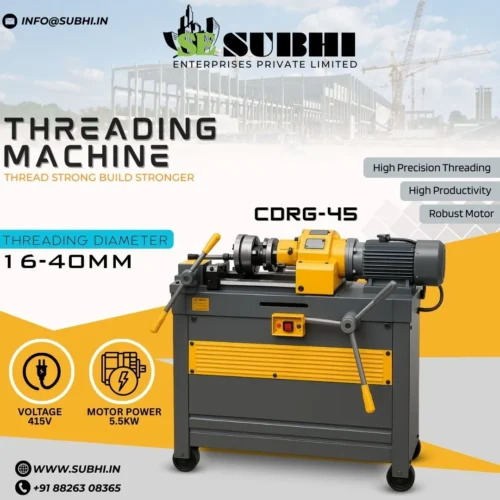
Why Rebar Threading Matters in Construction
Considered to be advantageous in many applications, including mechanical construction, working with machines, etc, type of processes such as these can bring change in creative development:
- Better Joints : Mechanical threading makes it possible to develop more robust joints than the ones made with lapped splices.
- Less Material Used : Overlap is reduced and this aids in saving steel in many construction projects which can be of great benefit for larger undertakings.
- Impervious Structural Integrity : Freedough threaded particulates allow for enhanced load concentration that is carried out in an available and effective manner.
- Efficiency space wise : Great for dense places with congestion of reinforcement where lapping cannot be done because it is not possible.
- Reduction in time : The process of joining steel rebars is made simpler and this in turn reduces the whole aspect of time in construction.
- Parts of a machine : components of a rebar with threads on the end
Key Components of a Rebar Threading Machine
Most Threading Machines possess a few core components, despite some variations from model to model/brand:
(a). Main Motor : These serve the purpose of controlling the speed and capacity of the threading.
(b). Threading Head/Die Head : This is the structure on the bar that cuts it into the rebar.
(c). Clamping Unit : Keeps the rebar in a secure place while the operation takes place.
(d). Coolant system : Keeps everything cool and lengthens the life of the tools resultant from prolonged use.
(e). Control Panel : These are useful for Operators that can start, stop and modify the machine’s configurations as required.
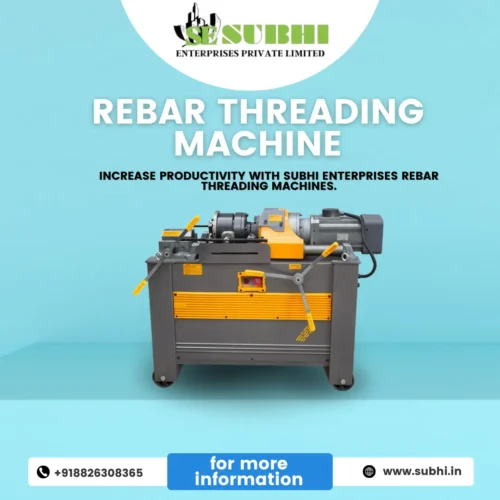
Operating a Rebar Threading Machine
A skilled operator makes the reap bar threading machine’s operation straightforward:
(1). Ram Preparation : Prior to threading, the rebar end using a cutting tool chamfering and straightening.
(2). Rebar Clamping : The operator puts the rebar portion on the clamping jaw unit, aligning it with the threading die.
(3). Thread Cutting : The machine is switched on, then the die head rotates toward the rebar, cutting thread along the rod.
(4). Final Inspection : The last thing to do is inspect the threads and check for errors of precision and uniformity.
Important Technical Specifications To Consider
When choosing a rebar threading machine, be certain to customize the machine according to the specifications given below:
FEATURE | DESCRIPTION |
---|---|
Rebar Diameter Range | Most generally goes from 16mm to 40mm while some other models extend to 50mm. |
Thread Pitch | Dependable machine grade; machine trimming options needs to allow customization |
Motor Power | Commonly powered between 4 kW and 7.5 kW. |
Threading speed | Cutting out time ranges 2-5 minutes for each bar end depending on bar size. |
Thread Length | 50-80mm is common and must match with coupler size. |
Weight | While stable heavy machines weighing 200-300 kgs are available |
Applications of rebar threading machines
Companies operating in nearly all sectors in the construction industry uses machines used to thread rebars:
1. Multi Storeyed buildings
Advanced grade rebar threading machines permits stronger joints in vertical columns and core walls.
2. Railways, highways and construction of bridges
In integrated threaded couplers used when erecting expressways, bridges, and flyovers, are assured to have Structural reliability under dynamic heavy load.
3. Dams and Power Plants
Threading machines used on massive rebar sections in other hydro projects beneift from non-permanent joints that offer seal proof and pressure resistent joins.
4. Metro and Railway Tunnels
Construction Underground projects aid enclose spaces with limited mobility while sorted threaded joints make for rebar connection in claustrophic spaces.
5. Precast Concrete Construction
The attachment of threaded rebars facilitates the assembly of precast parts, which enhances accuracy at the connections and enables lower costs in labor.
Safety Instructions for Using a Rebar Threading Tool
Even though it is a lot safer than operating a threading machine, having standards when using a rebar threading machine is very important.
Routine Upkeep Suggestions
(a). Daily Cleaning After every use, cleaning the machine helps prevent the accumulation of metal shavings.
(b). Lubrication Oil all moving sections occasionally to lessen friction.
(c). Check the coolant level and remove any debris from the tank consistently.
(d). Inspect die heads for any necessary replacements and check for tear and wear.
(e). Unusual sounds of the motor and undesired temperatures during prolonged use should be monitored.
(f). Always check the temperature to ensure motor health.
Selecting The Best Threading Tool For Rebars
Always remember these factors before purchasing a machine:
(1). Small portable machines would work for small jobs but larger high capacity models are needed for bulk construction sites.
(2). Make sure the machine supports all the bar diameters used, consider compatibility for bar diameter.
(3). Make sure your chosen model matches your workstation’s power source, commonly 3 phase power, understand the significance of power supply.
(4). Focus on well known brands avalaible in the market that sell replacement parts and are known for reliable support services after selling.
(5). Focus on trustable dealers who will provide spares and cuts not only for parts but also cuts for off work hours, ensuring reduced idle time.
Final thought
Rather than just an optional luxury for construction projects, a rebar threading machine is an increasingly popular tool. It will always help build strong enduring structures, no matter what you’re working on; a dam in the Northeast, a metro tunnel in Delhi, or a Mumbai skyscraper.
As with any construction involved, the integration of rebar threading machines sustains productivity, while simultaneously increasing the structural strength and safety, alongside upkeep with adjacent cutting and prepping machines. Construction is ever-changing and becoming more automated and sustainable, so the integration of rebar threading machines gives businesses a major competitive edge.
If you have not decided on a model for a rebar threading machine, consider external factors. Every selection should view long-term objectives and emphasize project specifics, so every model comparison becomes a strategic decision. With the right tools, every threaded bar becomes a vital component in advancing construction systems.